
CO2 footprint management
In the well-known optimization scenarios of the supply chain, optimization is usually based on conventional KPIs. To name a few examples: Cost, lead time, availability, turnover, .... We believe that the consideration of the carbon footprint will play an increasingly important role in the evaluation of alternative solutions in the future. Accordingly, the search will no longer be limited to the most effective solution in terms of time and costs, for instance, but also to an alternative solution that is optimized in respect of its CO2 footprint.
The following use cases, for example, would be suitable for such an optimization scenario:
Optimize transport routes
We evaluate the CO2 footprint of transport routes and means of transport. Alternative transport options can thereby be compared in terms of CO2 consumption.
Inventory optimization
We evaluate the Product CO2 Footprint for each SKU. This describes the greenhouse gas emissions generated during the production or procurement of a product. Which products are held in stock can therefore be decided not only on the basis of the contribution to the delivery service level, but also on the contribution to the overall footprint of the portfolio.
Evaluate replenishment alternatives
In addition to a classic make-or-buy decision, the question of HOW something is manufactured and from WHERE the goods are procured is examined. The alternatives are thereby evaluated in the search for an optimal solution not only after procurement costs and replenishment lead time, but also after CO2 costs.
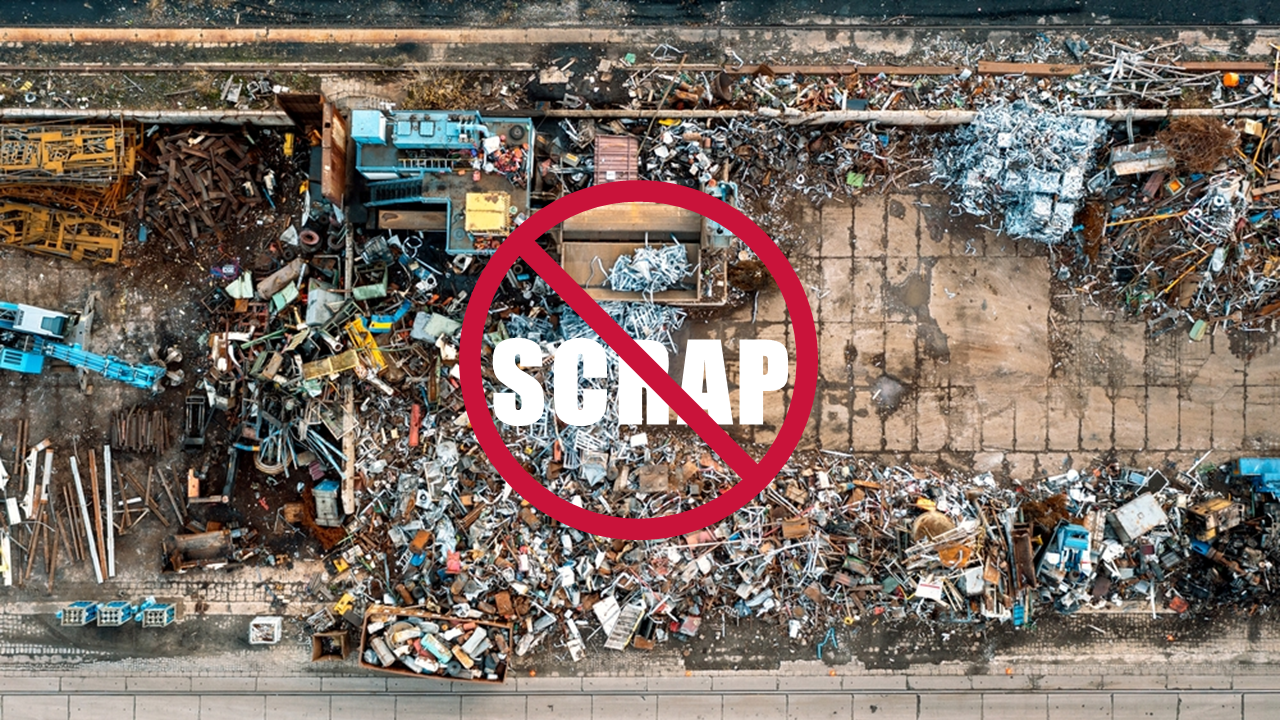
Avoiding waste
Scrapping goods that can no longer be sold or materials that can no longer be processed is both economically and environmentally painful. Manufacturing or procurement has tied up resources and incurred costs that are not balanced by any use or revenue. Therefore, in a sustainable planning approach, unneeded inventories should be reduced as far as possible or, in the best case, avoided entirely.
There are several planning strategies for avoiding scrapping:
Demand-driven manufacturing
Demand-driven manufacturing is usually faced with competing goals in terms of capacity utilization or availability for sales. But there are now planning processes that take these goals into account in a balanced way. The correct dimensioning of buffer stocks and batch sizes play is a crucial factor in this. Demand-Driven MRP is a prominent example for such an approach.
Reduction of safety stocks
Safety stocks are still a popular instrument for ensuring availability. However, these are usually statically defined and can quickly lead to overstocking in the case of little-used or discontinued items. In addition to safety stocks, there are numerous alternative methods for generating safety in the event of fluctuations in demand.
Early Phase-Out Planning
When the life cycle of an item or component is nearing its end, certain actions should be taken in planning. If this does not happen in time, there is a high probability that unneeded goods will continue to be ordered or manufactured. Well thought-out phase-out planning protects against the waste of resources and costs.
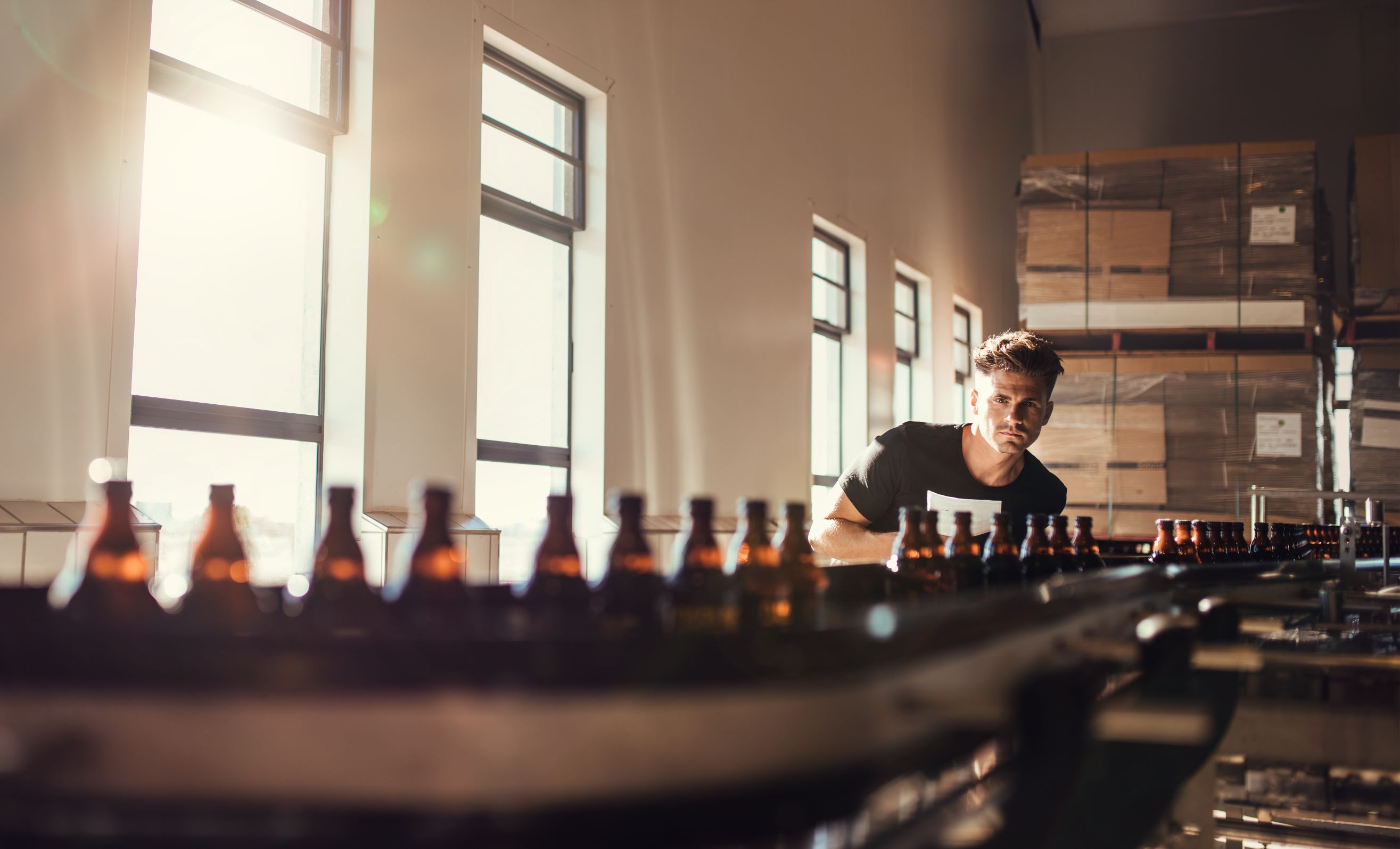
Reuse & Recycle
In the consumer goods and food industry in particular, goods and their packaging are thrown away after use or when they are broken, and new ones are bought. In the long term, this is not a sustainable approach to manage resources. Therefore, there are developments and ideas in many areas to return and recycle used or broken goods and their packaging. One of the most well-known and already established methods is the deposit system for returnable bottles. But there are also approaches to returning used consumer goods, such as washing machines, back to the manufacturer so that individual parts can be reprocessed. Or a service is offered to repair broken goods as an alternative to buying new ones.
These processes, some of which are still very new, should be taken into account in sustainable planning:
Planning deposit systems
The return of refillable bottles is already causing challenges for the beverage industry. Planning of the returned quantities is essential for the procurement planning of new, unused containers. Cleaning processes and sorting should also be taken into account in planning before the returnable container is available for reprocessing.
Return and recycling of used goods
When planning the return and reuse of used goods, it is investigated which goods are returned after which period of time and how often. In addition, it is examined which components can be recycled afterwards. On the one hand, a forecast of the return rate is determined and the return process must be integrated into the operational planning.
Repair service and spare parts planning
There are two main challenges to planning a repair service: First, a return rate must be determined to define the need for service capacity. And secondly, for the procurement and provision of spare parts, it is necessary to investigate which parts break and how often. From the investigation, it can be derived whether it is worthwhile to stock certain spare parts.